A while ago I got a dowel maker. Got it up and running, and made a video of making a ¼ inch beech dowel.
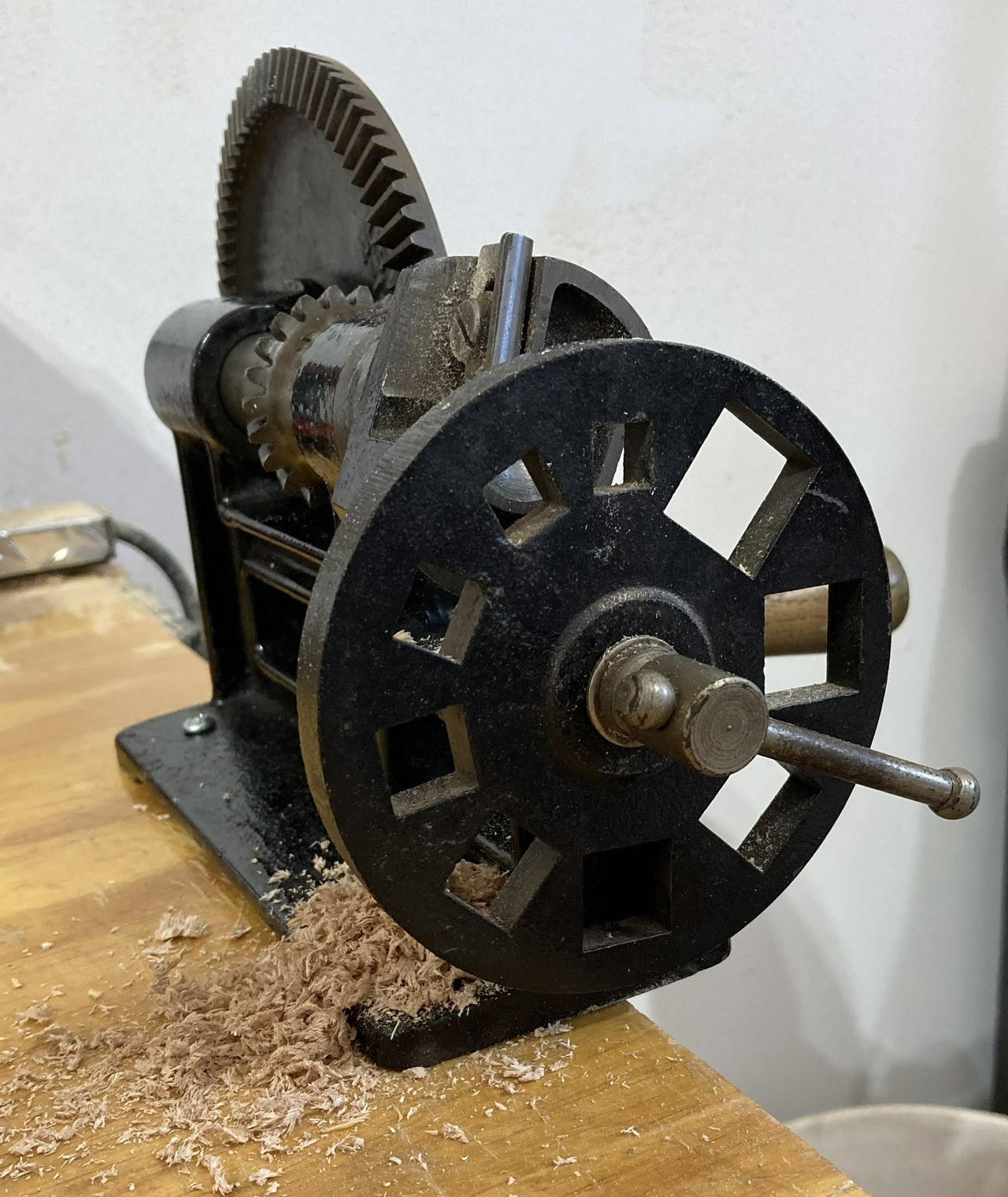
And here's a photo of the instruction sheet.
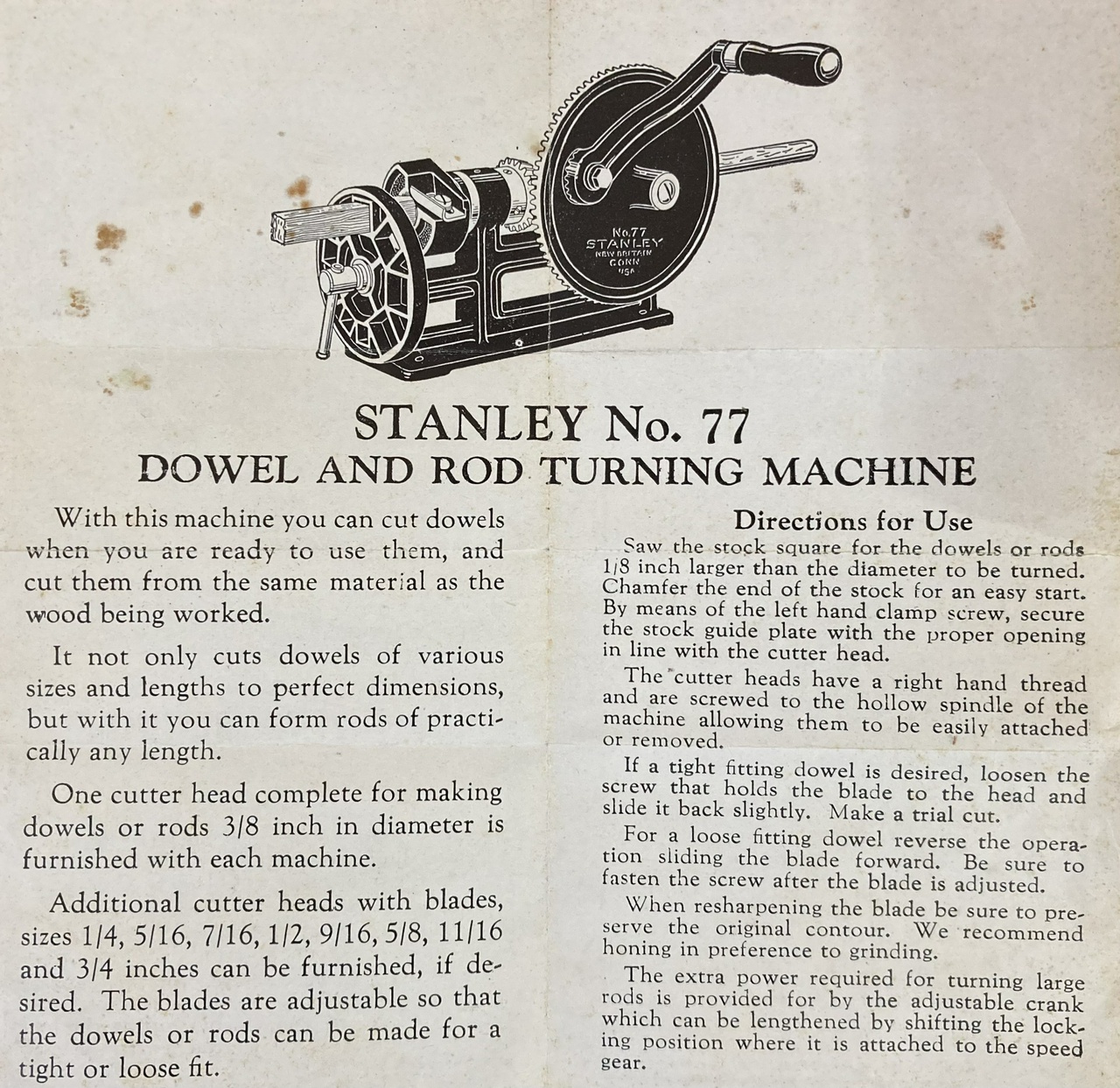
Stanley No. 77
DOWEL AND ROD TURNING MACHINE
With this machine you can cut dowels when you are ready to use them, and cut them from the same material as the wood being worked.
It not only cuts dowels of various sizes and lengths to perfect dimensions, but with it you can form rods of practically any length.
One cutter head complete for making dowels or rods ⅜ inch in diameter is furnished with each machine.
Additional cutter heads with blades, sizes ¼, 5/16, 7/16, ½, 9/16, 5/8, 11/16 and ¾ inches can be furnished, if desired. The blades are adjustable so that the dowels or rods can be made for a tight or loose fit.
Directions for Use
Saw the stock square for the dowels or rods 1/8 inch larger than the diameter to be turned. Chamfer the end of the stock for an easy start. By means of the left hand clamp screw, secure the stock guide plate with the proper opening in line with the cutter head.
The cutter heads have a right hand thread and are screwed to the hollow spindle of the machine, allowing them to be easily attached or removed.
If a tight fitting dowel is desired, loosen the screw that holds the blade to the head and slide it back slightly. Make a trial cut.
For a loose fitting dowel reverse the operation, sliding the blade forward. Be sure to fasten the screw after the blade is adjusted.
When resharpening the blade be sure to preserve the original contour. We recommend honing in preference to grinding.
The extra power required for turning large rods is provided for by the adjustable crank which can be lengthened by shifting the locking position where it is attached to the speed gear.
I have cutters for the even sixteenths, which I think should cover my needs pretty well. Anything larger than that, I can make on the lathe. And if I should need one of the odd sixteenths, I can chuck a dowel of the next larger size in a drill and sand it down until it fits.
I also had a buddy ask how I have the cutters set up. Here are a couple pictures.
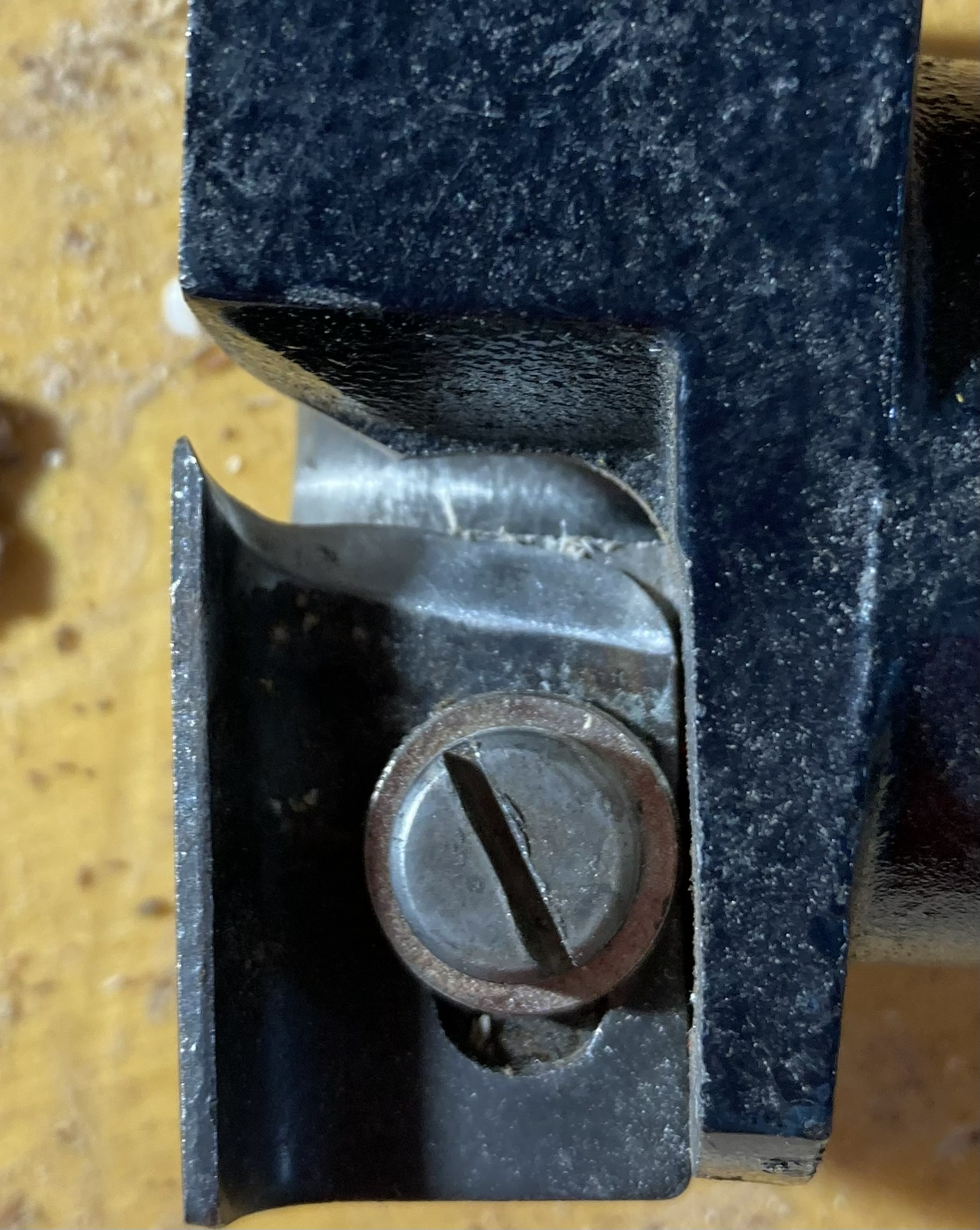
The left half of the blade is exposed over the edge of the cutter body. The right half isn't. Note that on mine, the blade can pivot a little, and it's very sensitive to pivoting, but it looks like years of sharpening has also made the edge of the blade kinda curved.
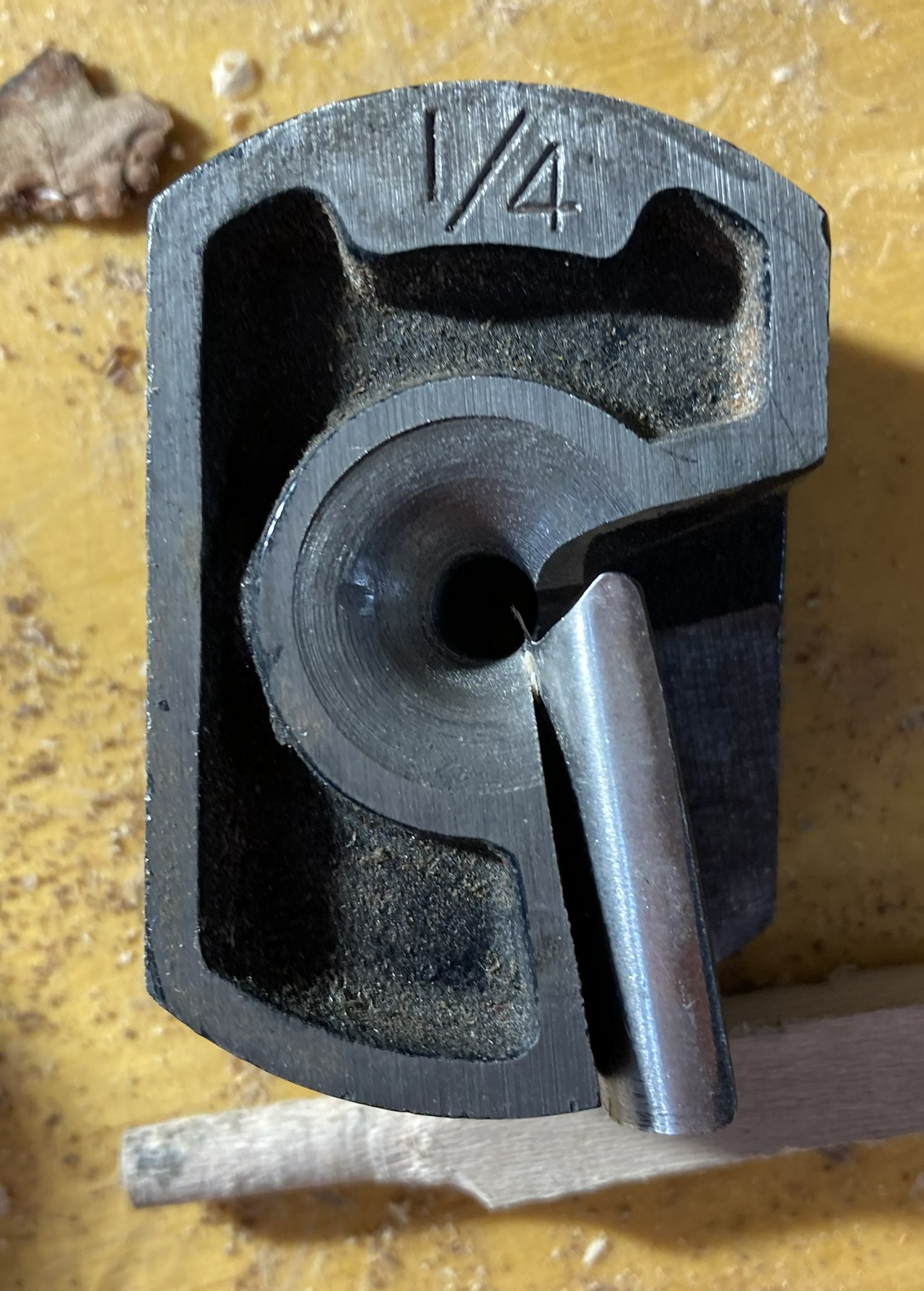
This one also shows just how little of the blade is protruding beyond the body of the cutter. I can back it off a hair and get an even better finish, but I suspect the real trick is that the blade is skewed a bit from a straight peeling cut, and that improves the finish, just as it would when using a skew on the lathe.
Set up like this, the dowels end up being about 1/128 inch oversized, but a quick wipe down the length of the dowel with some 60 grit sandpaper makes them fit the holes drilled by my auger bits perfectly. I would rather have the dowels slightly tight than too loose, since it's much easier to make them looser than tighter.
I also bought three brand new blades, and as the blades are identical across all the cutting heads, that should be a lifetime supply for me.
Contents
#woodworking #tools
Discuss...
Reply to this in the fediverse: @davepolaschek@writing.exchange