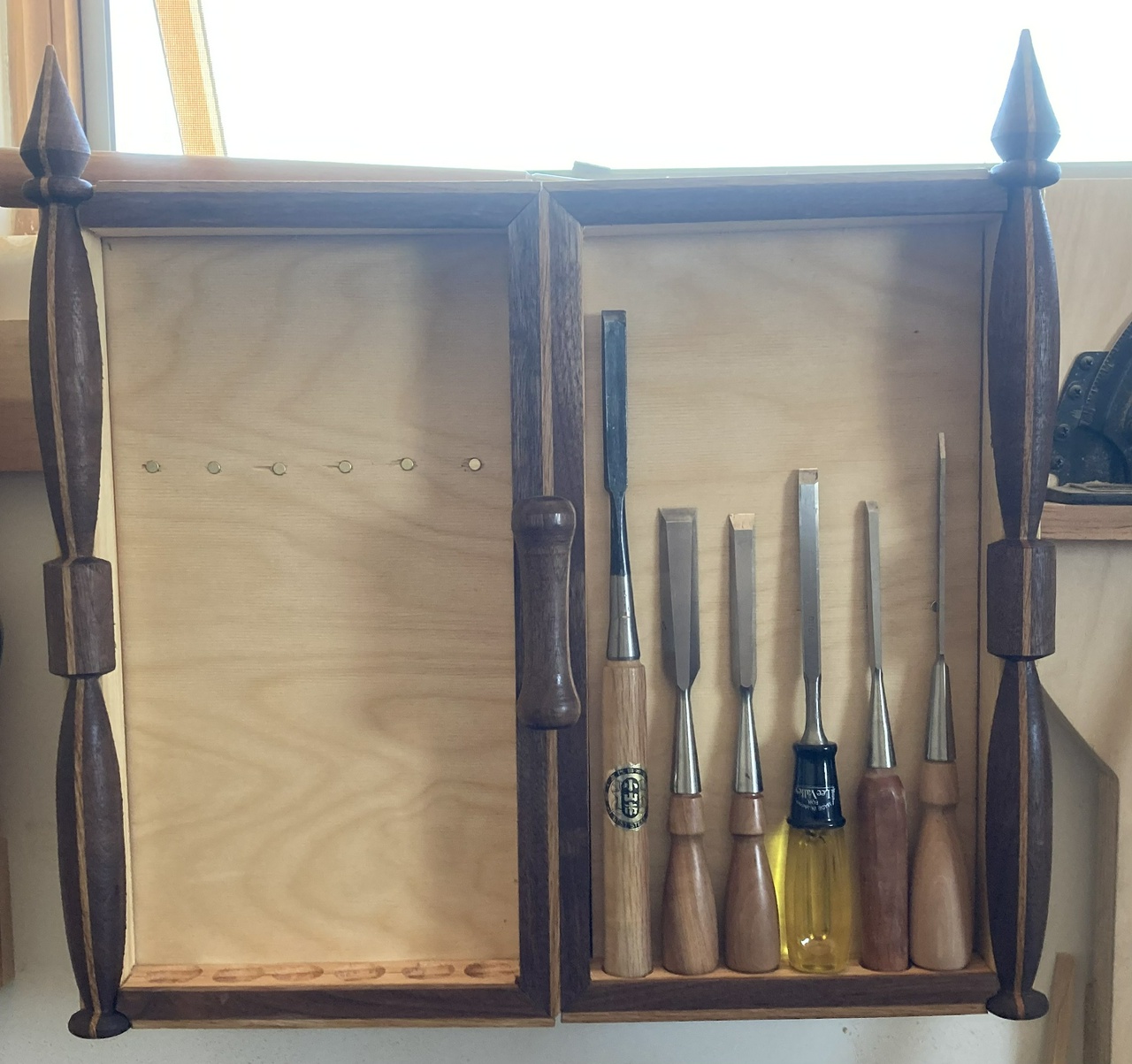
Over the past few weeks I built a till to hold all of my chisels and gouges, and here it is. It had a total of five rows of tools, and each tool sits in a one inch diameter hollow, with the sharp end of the tool held to the panel behind it by a 3mm x 6mm rare earth magnet.
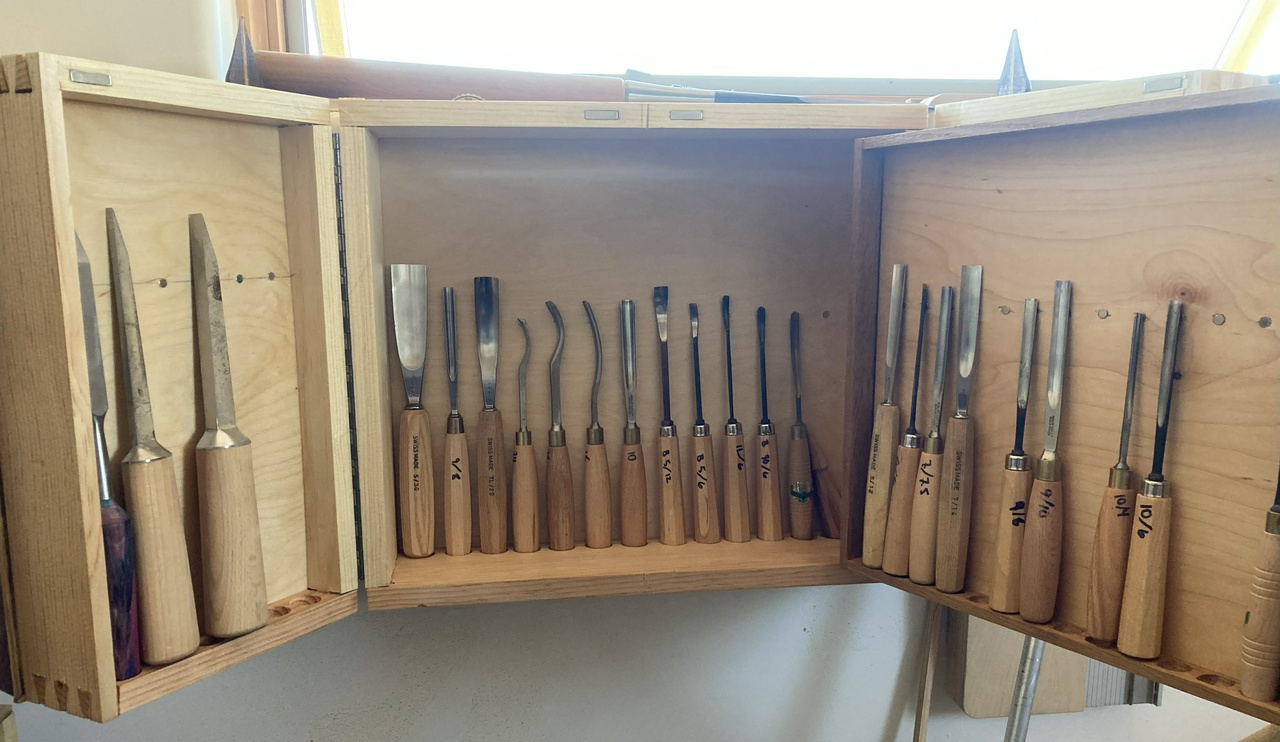
The back row (farthest inside) holds my bent gouges and spoon gouges. They’re not used very often, so hiding them deep inside is fine. Opposite them are straight gouges in higher curvatures. I use them pretty often, so this isn’t ideal, but I’ll get things sorted better over time.
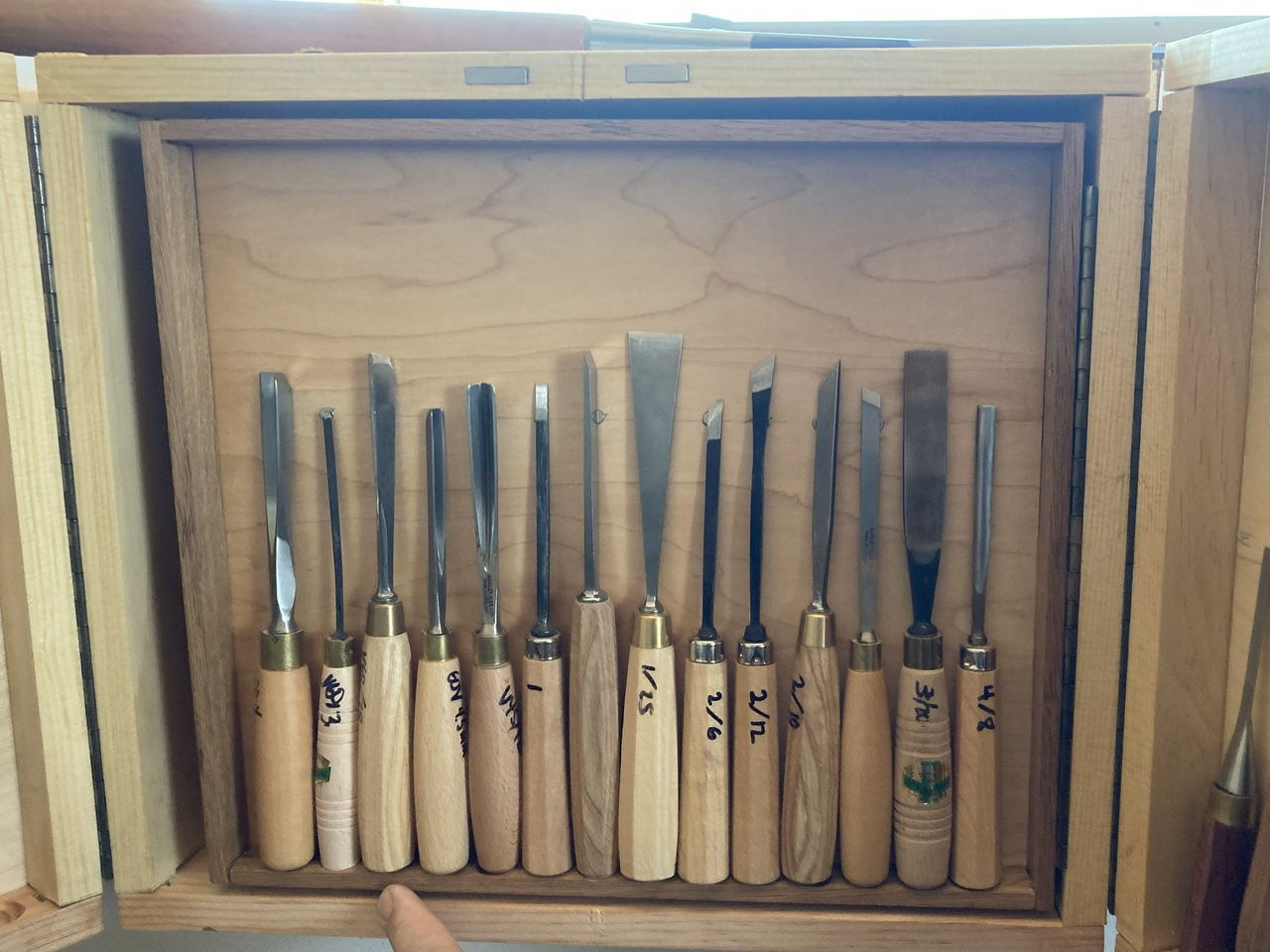
On the outside of the inner door of the storage are the straight gouges and lesser curves. Also the V gouges are here, as I use them fairly often.
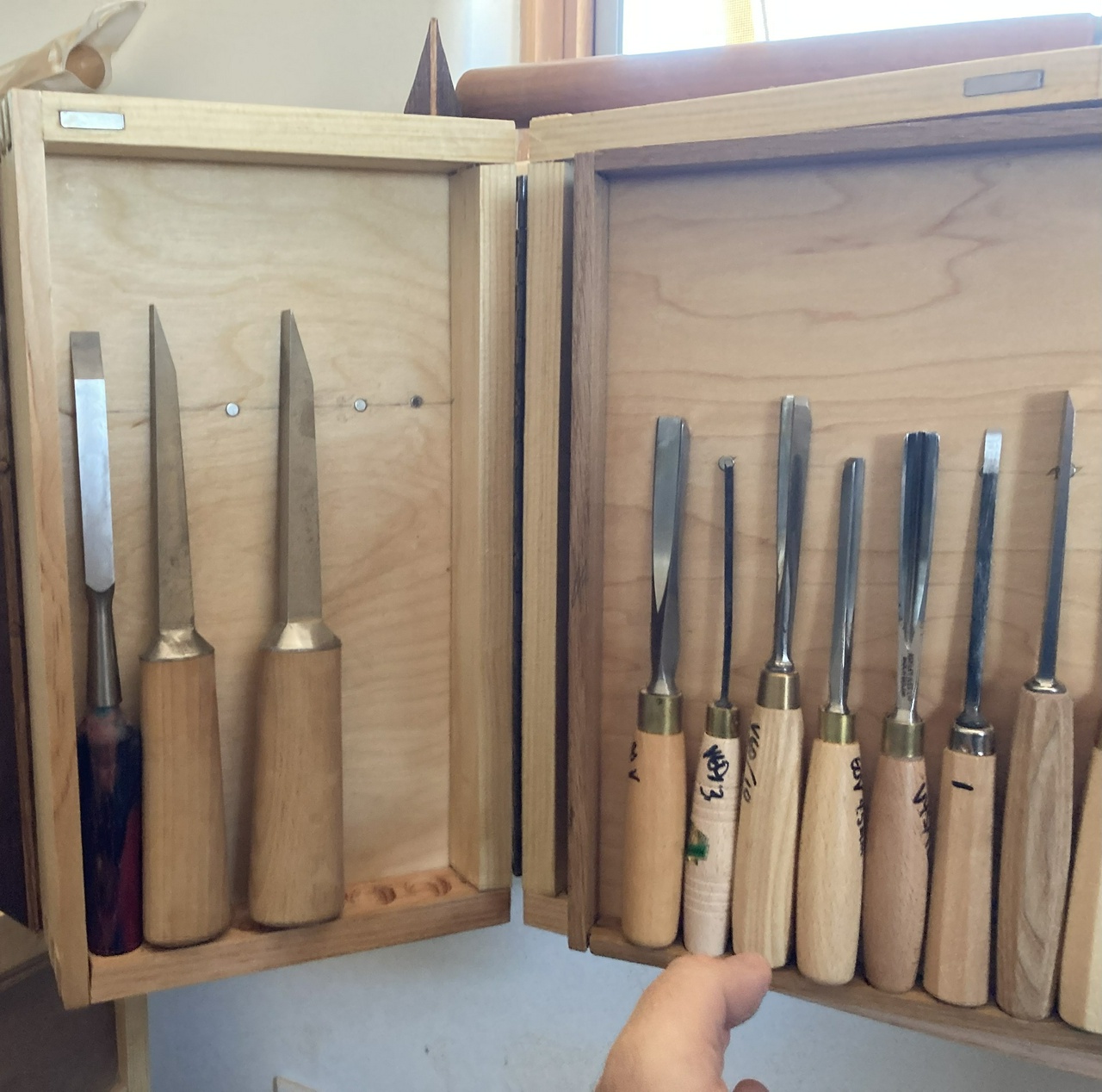
On the inside of the left door are my mortise chisels. Again, not frequently used, and probably these should move to the inside of the inner door.
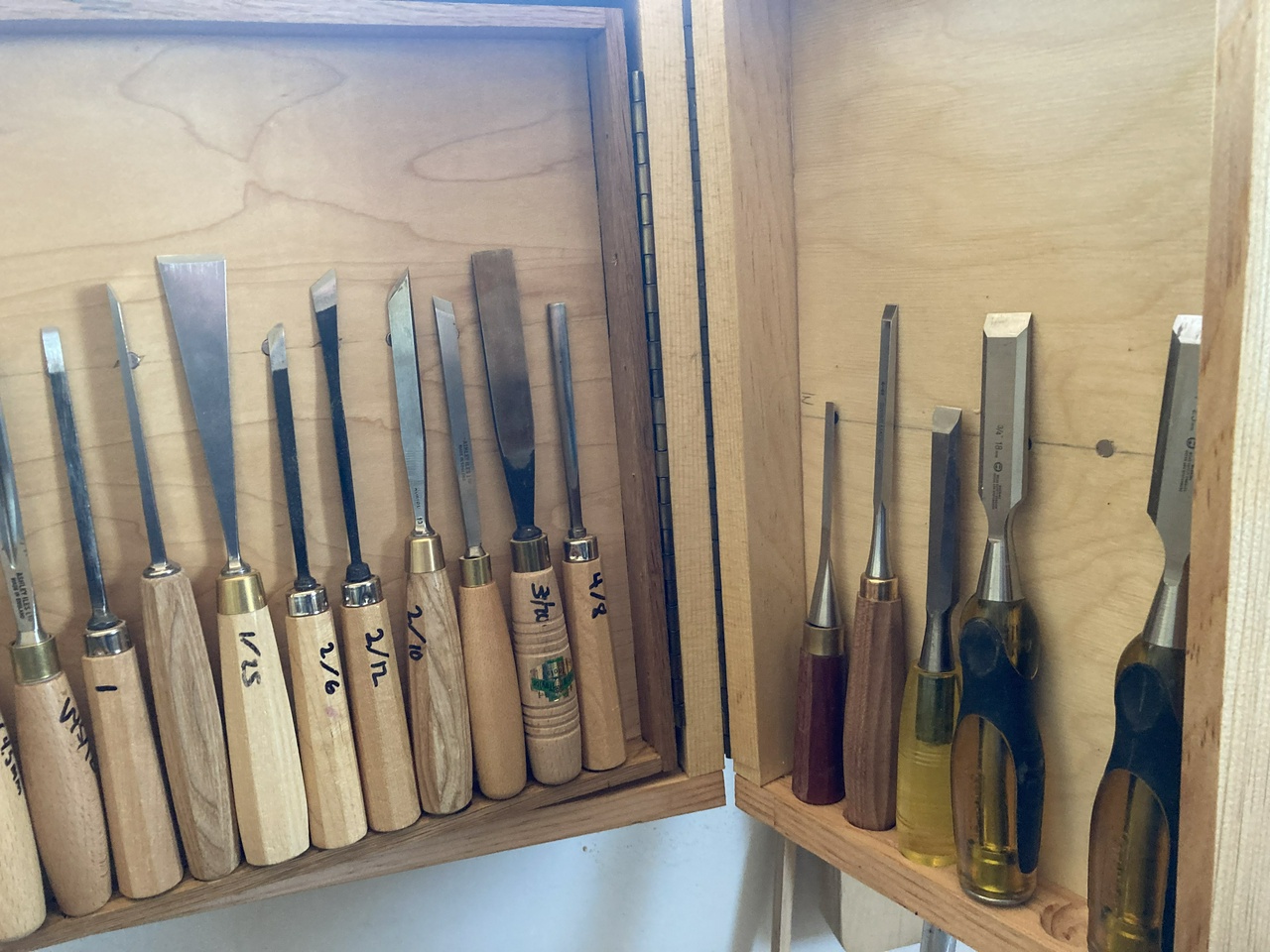
On the inside of the right door, I have seldom-used chisels. These are spares, and again could move farther in.
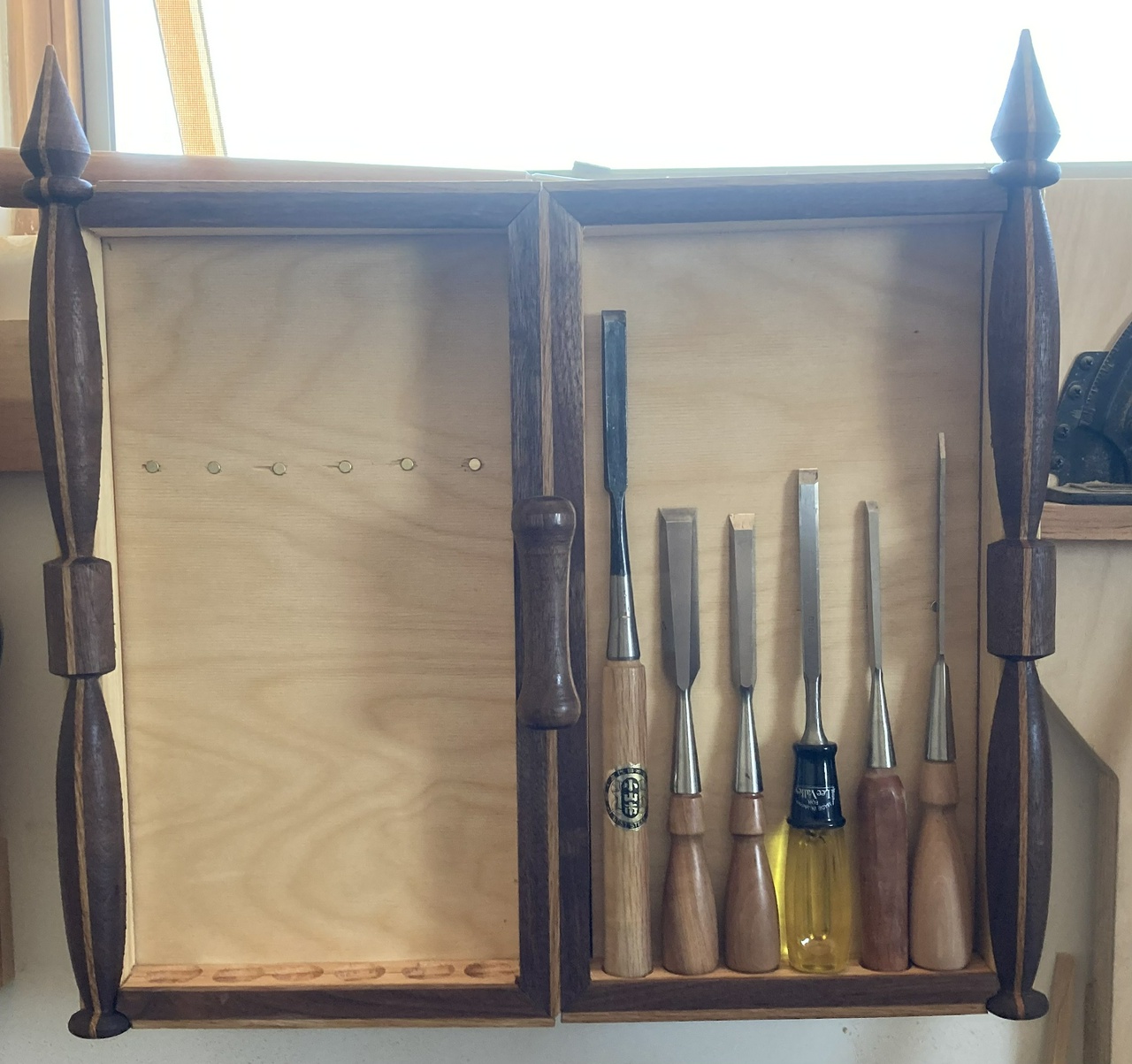
And finally the outsides of the doors hold the normal bench chisels which I use most often.
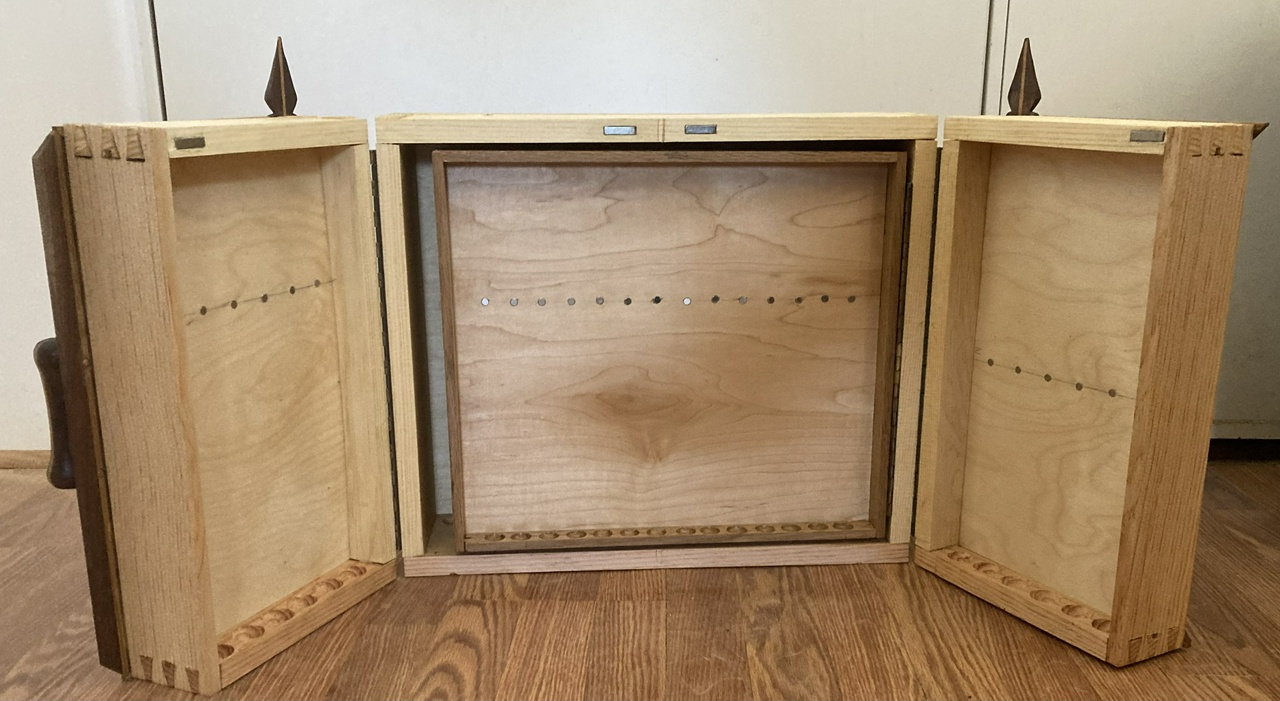
Construction of the carcasse is pine with Baltic birch panels.
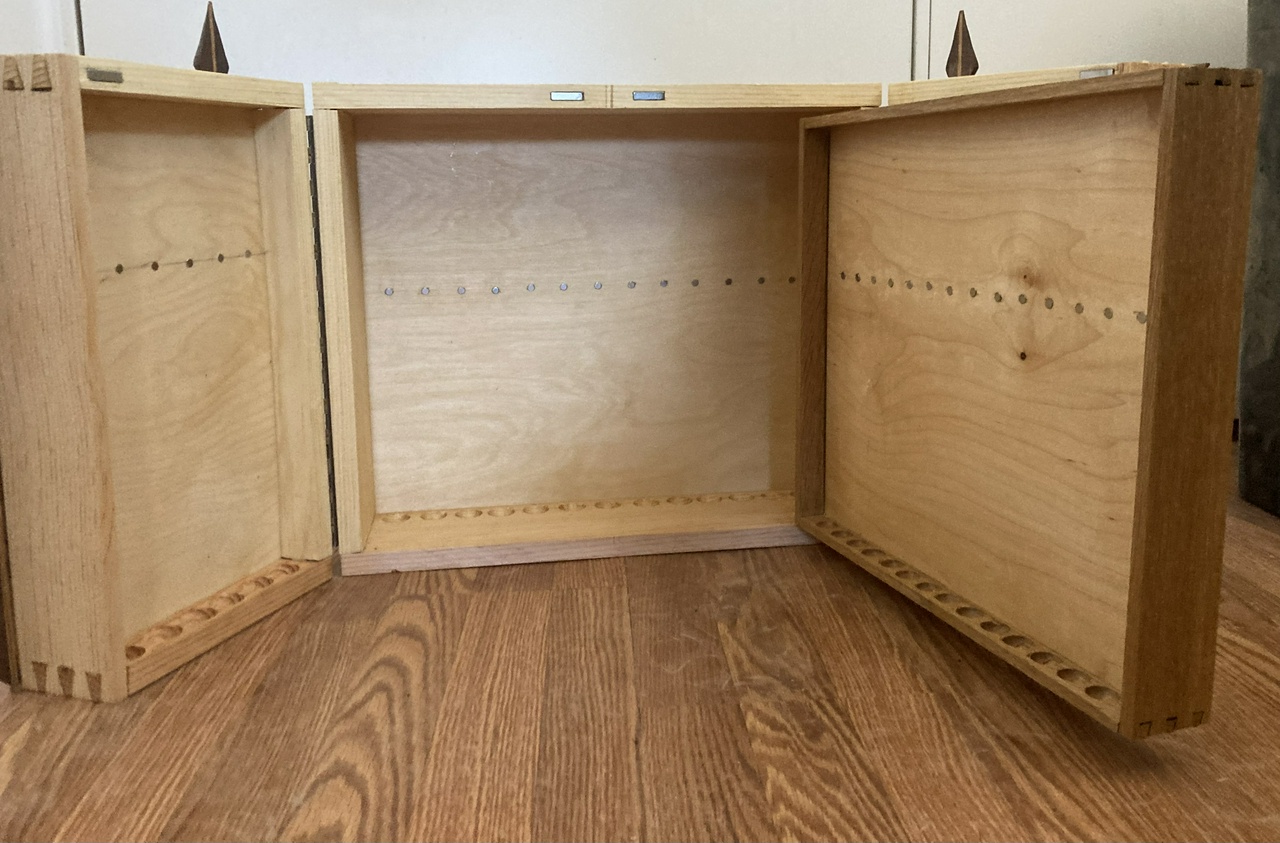
The inner door is white oak, also with a Baltic birch panel.
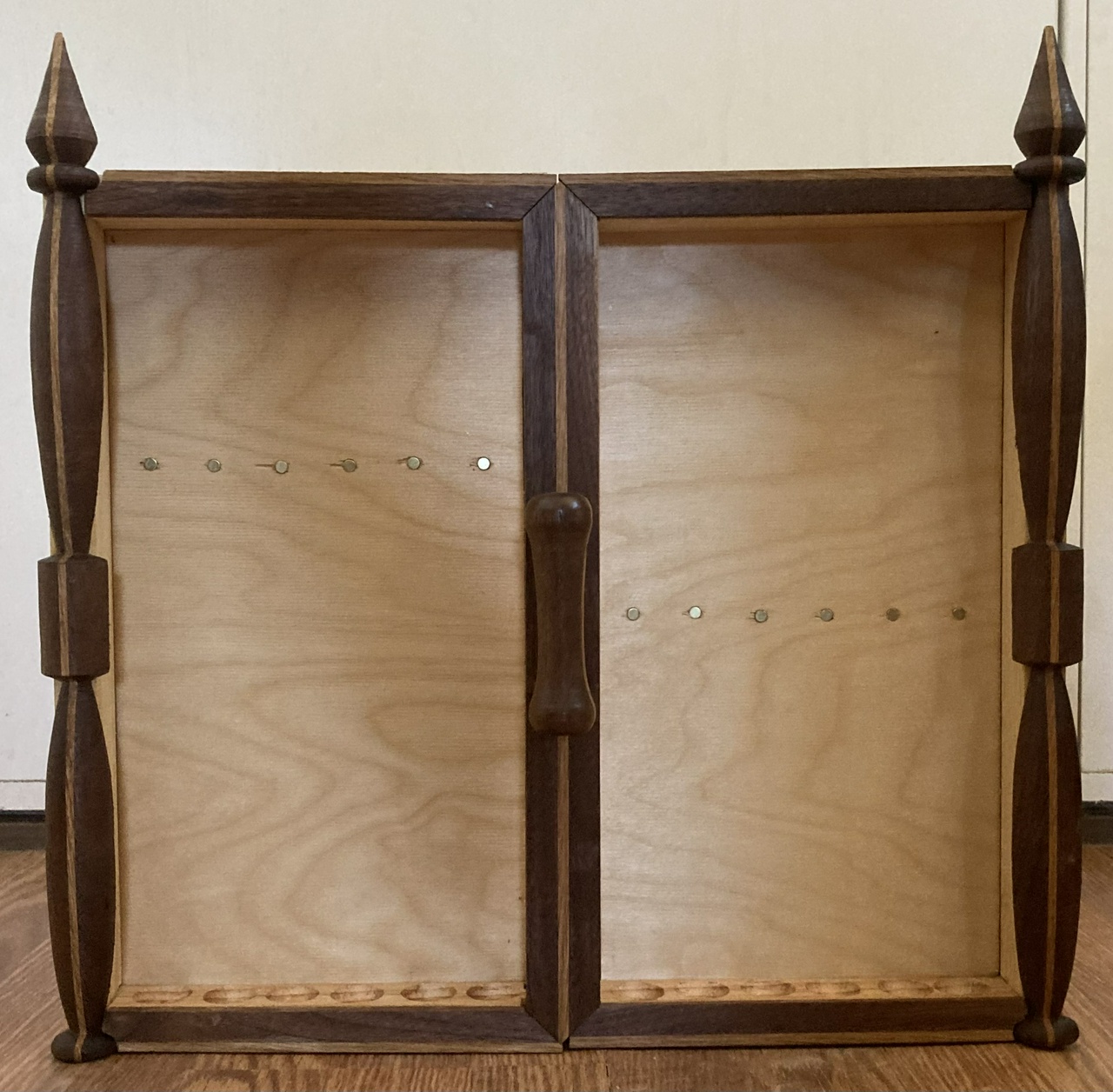
The outer doors have decorative bits made from walnut and oak, partly to make the till a little prettier, but also so I could practice turning the decorative turnings and mitering the flat bits. Shop furniture is a great way to practice my skills.
The carcasse was built first, then sawed open to remove the doors. Then I drilled holes for the piano hinge for the inner door. I then sawed the two doors apart and aligned and mounted the piano hinges for the inner door, then the outer doors. I applied the trim, cleat on the back, and then coated everything with a coat of tung oil.
#woodworking #projects
Discuss...
Reply to this in the fediverse: @davepolaschek@writing.exchange