This is a smoothing plane I made for the 2019 Spring Surprise Swap.
My recipient was Jerry, aka Turns4Wood The plane body is a sandwich of birch, African mahogany, and elm with an ipe sole. The elm was spalted and has been stabilized. The wedge is pear. The blade is at 45°︎ so it's fairly general purpose.
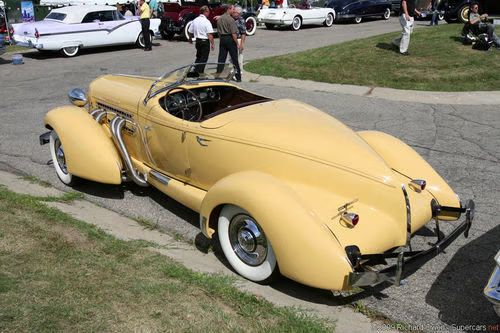
The looks of the plane are roughly based on a 1935 Auburn Speedster. I think that's a pretty good looking car, and kept it in mind while I was shaping the plane body. I think I did ok, and definitely a lot better than my first try, which looks more like a VW Beetle.
The plane uses the Veritas small plane kit with an O-1 blade.
Rough shaping was done with a bandsaw, then a belt-sander, and finally hand-sanding using the sanding blocks I got in one of my first swaps. Thanks again for those, Pooh!
The wedge is a piece of stabilized pear. I got the pear from HokieKen, and it was pretty soggy, so I wasn't sure if it would stabilize well, but I dried it in the oven without it cracking, and after it was stabilized, I carved in my mark. Until now I had burned the mark using a small laser engraver, but that died so I carved it by hand, and then filled the carved lines with black wood filler. I need some more practice carving.
I sanded up to 240 grit. Finish is two coats of linseed oil, followed by three coats of blonde shellac.
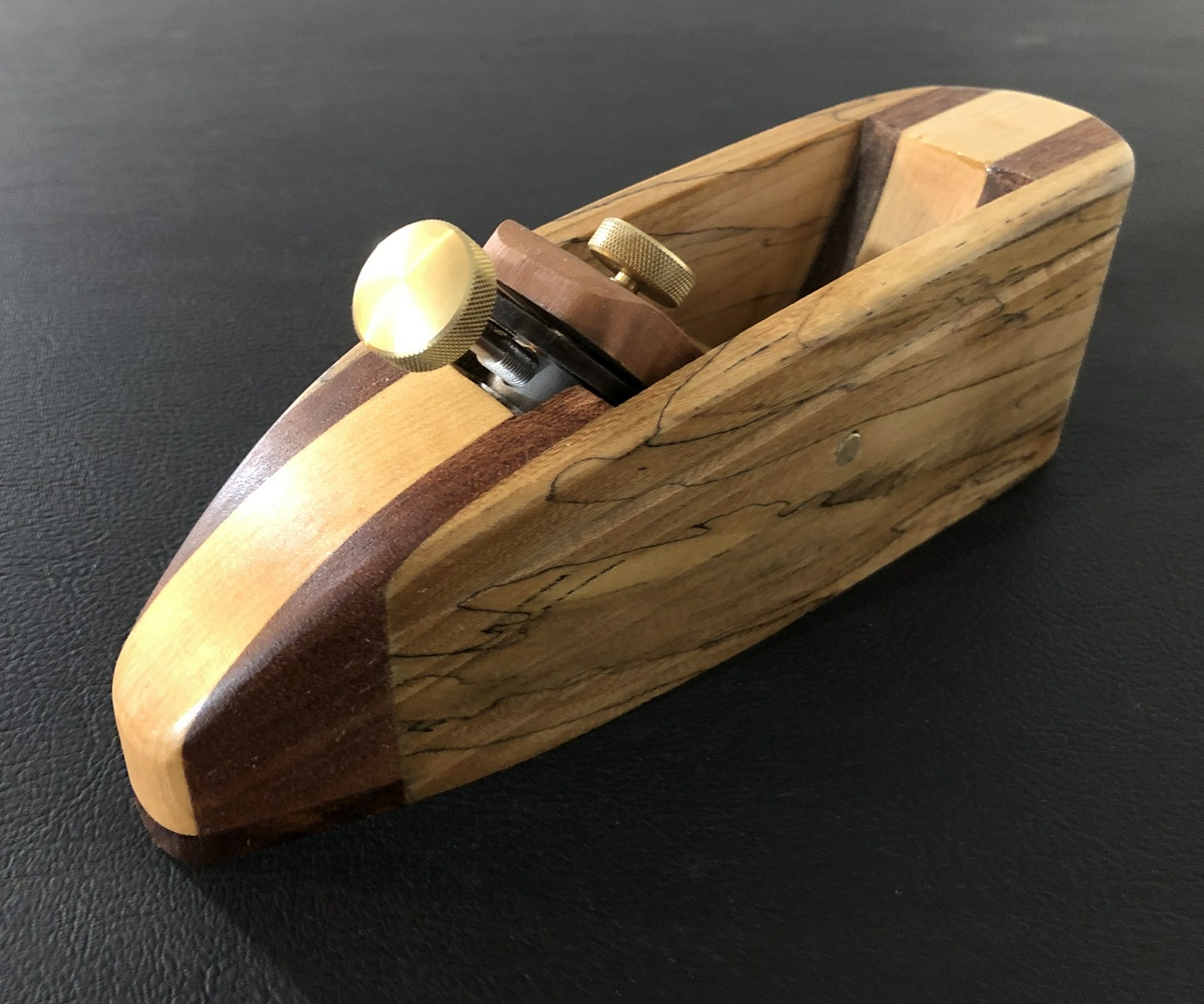
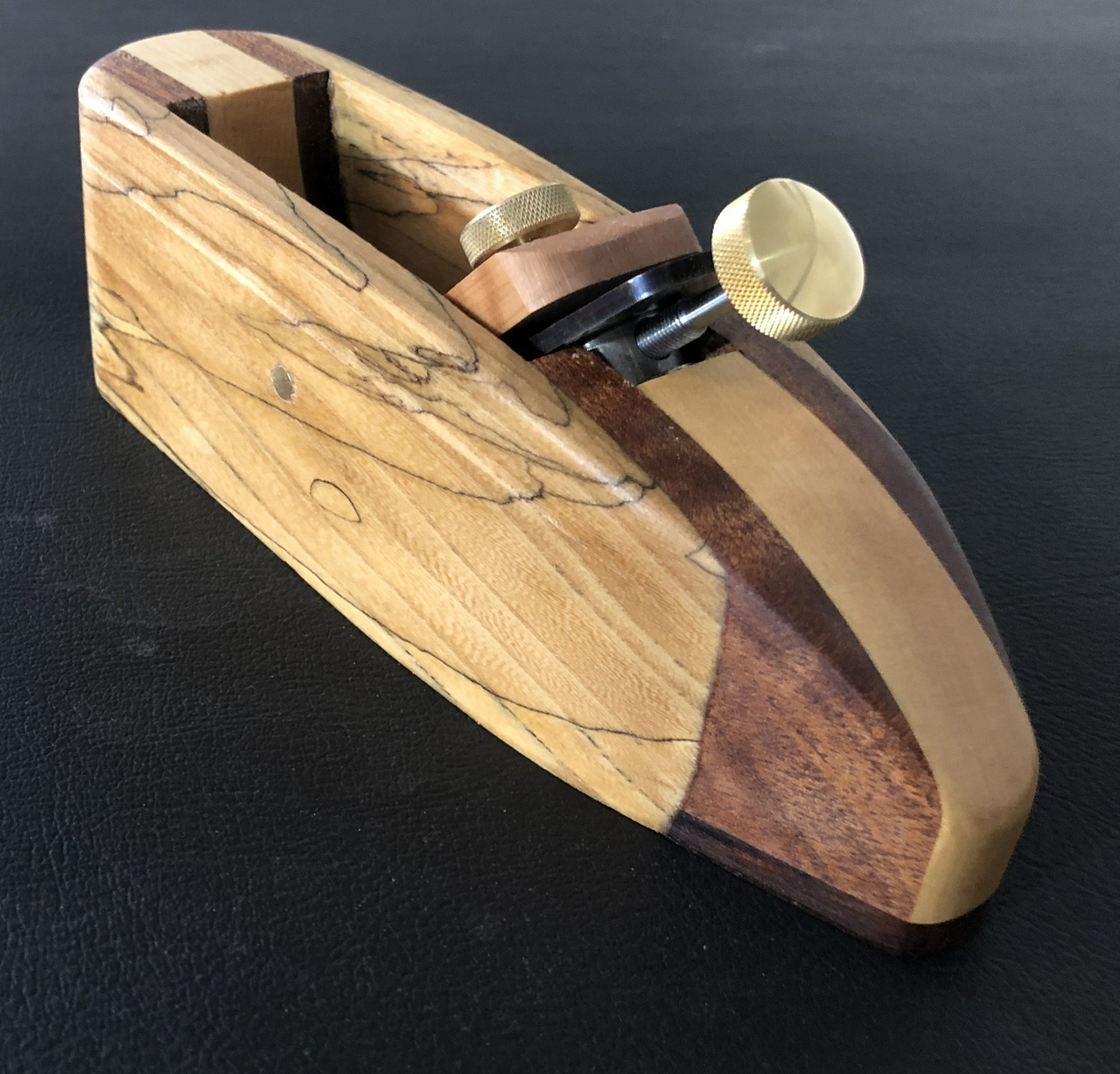
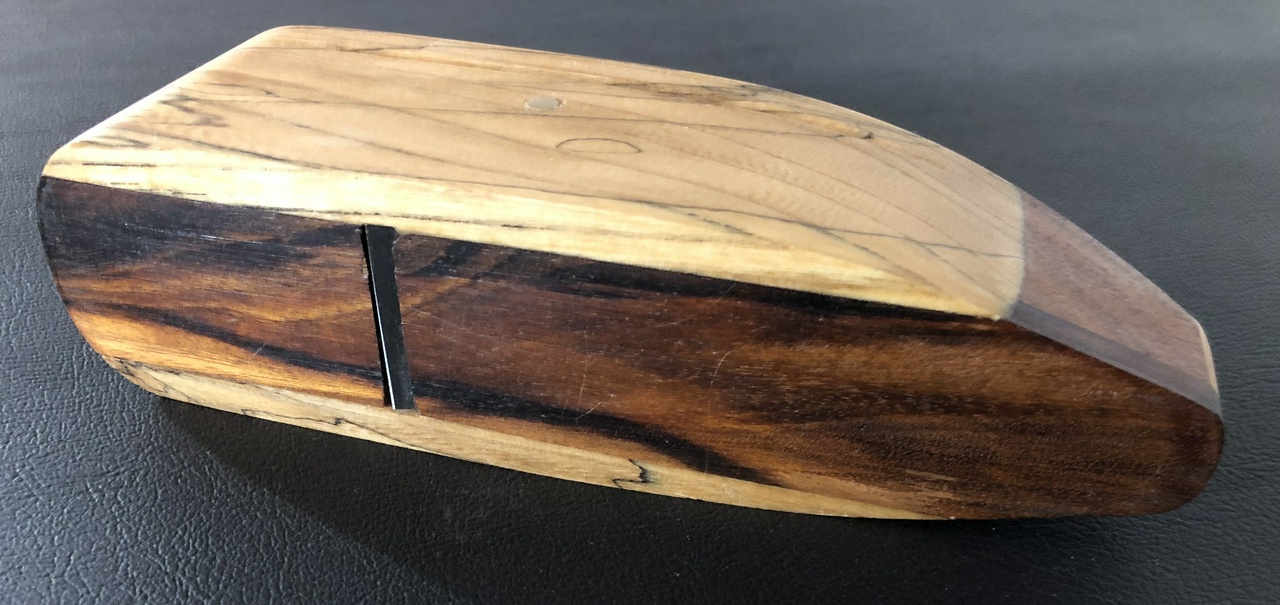
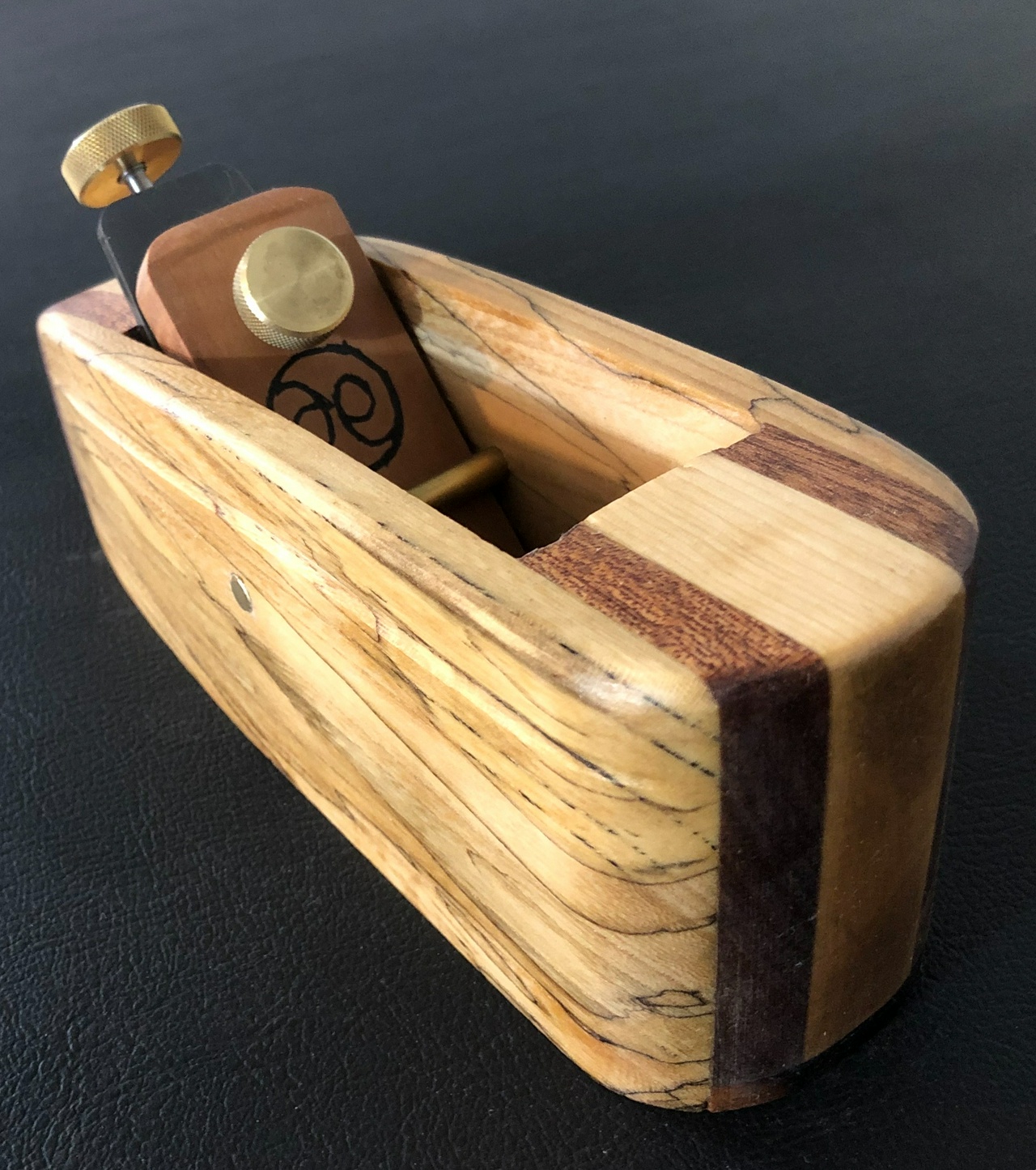
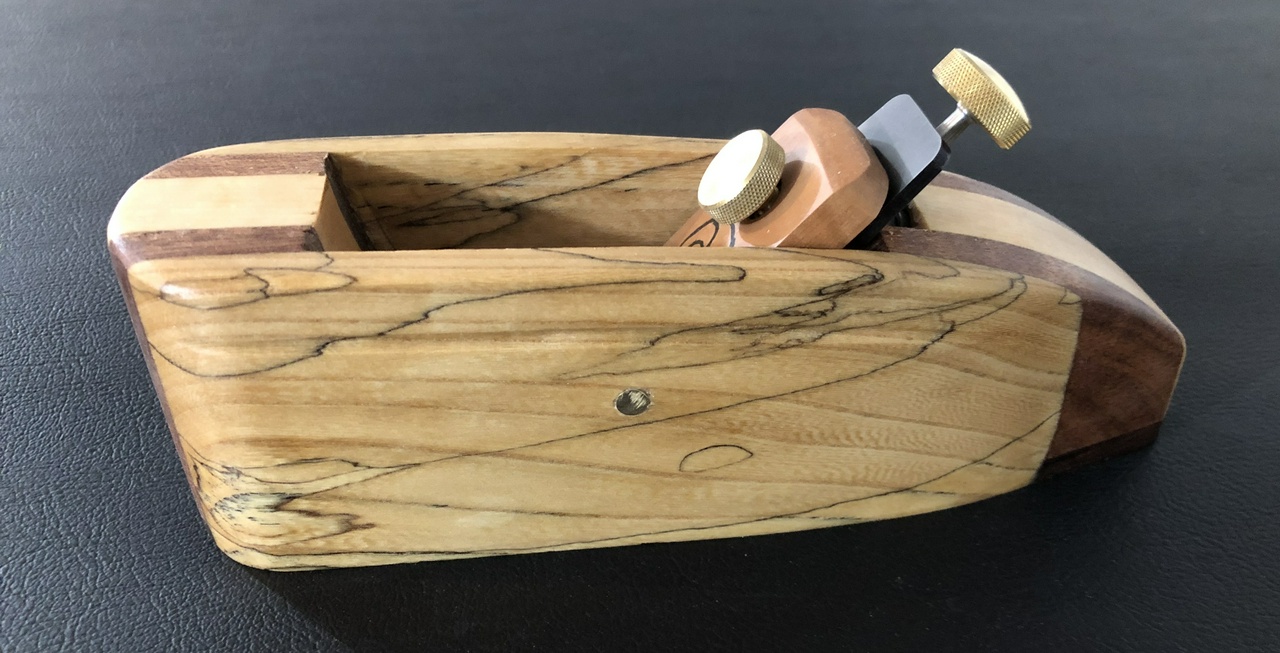
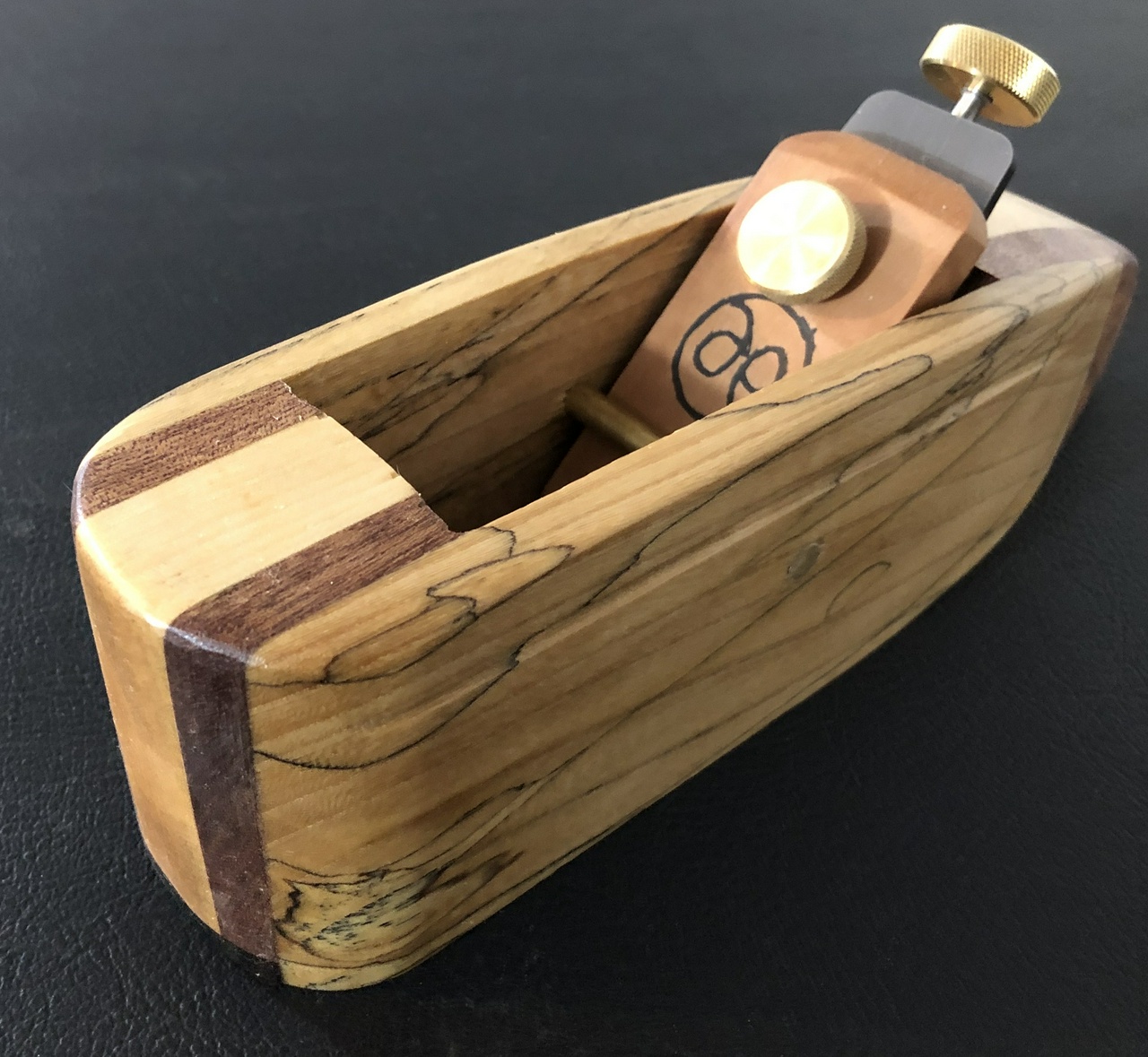
I sent the plane to Jerry in a hand-made wooden box. The box is butternut sides, a pine bottom, and an African mahogany top.
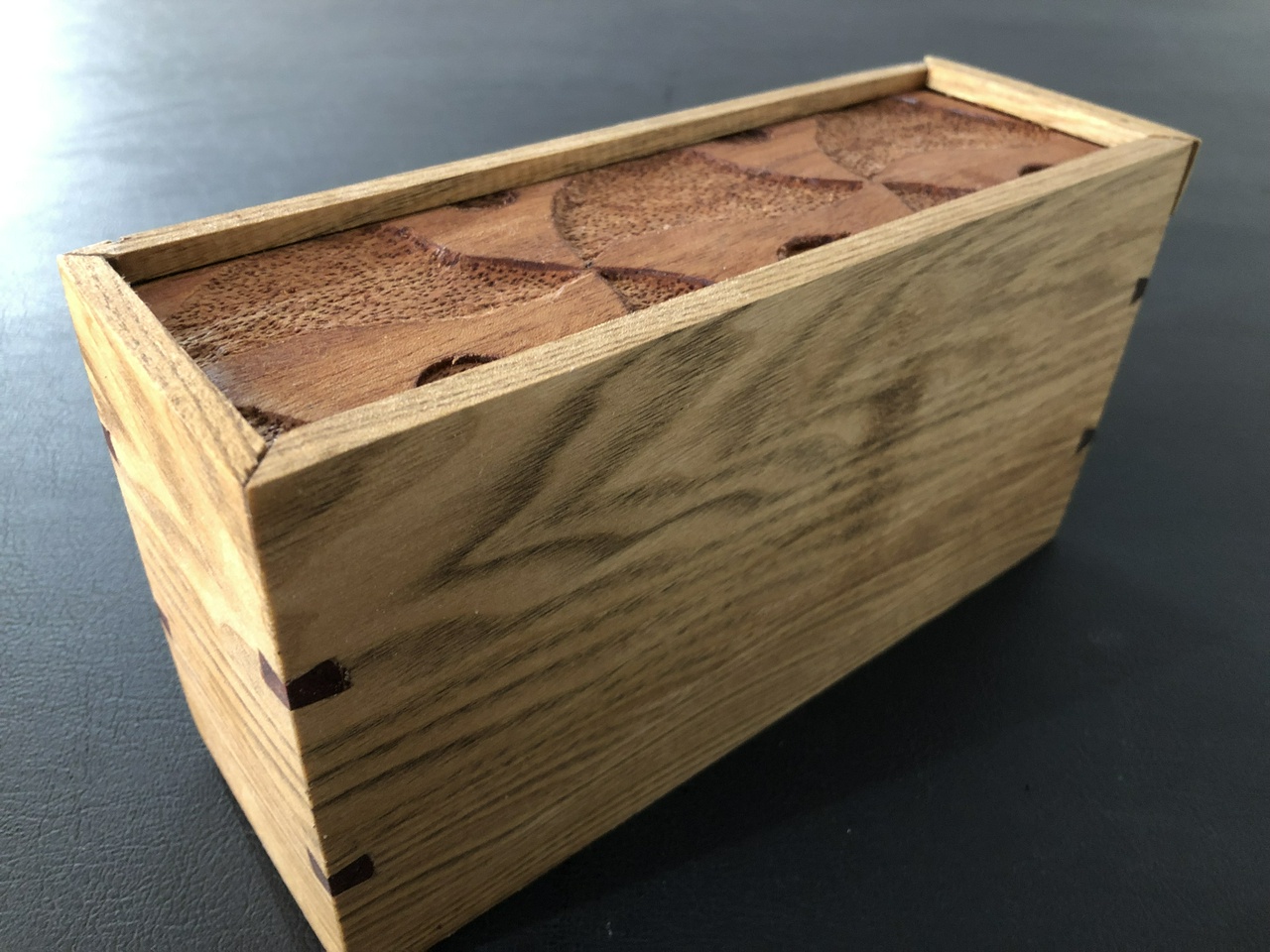
I carved the lid based on a pattern from the Alhambra in Granada, Spain.
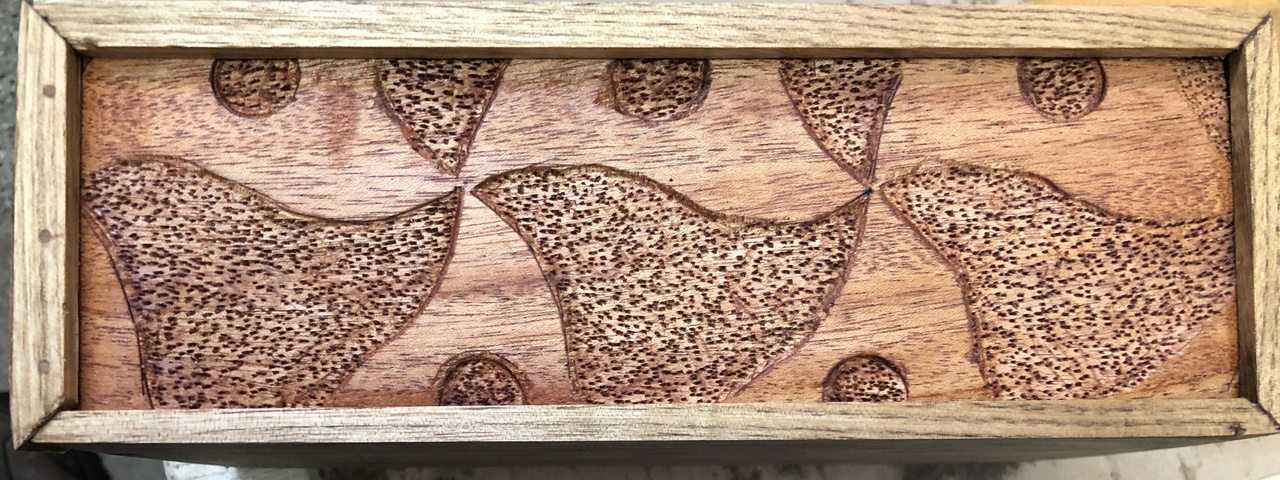
I got the details on how to construct the pattern using a compass and straightedge from the book Islamic Geometric Patterns.
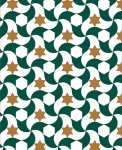
The splines in the corners are some eucalyptus from Arizona I got from HokieKen, who got it from AZDave, who got it from AZWoody (part of the fun of swaps is the bonus items included and I try to pass on wood I've received in previous swaps). I thought it would offer a nice contrast to the butternut.
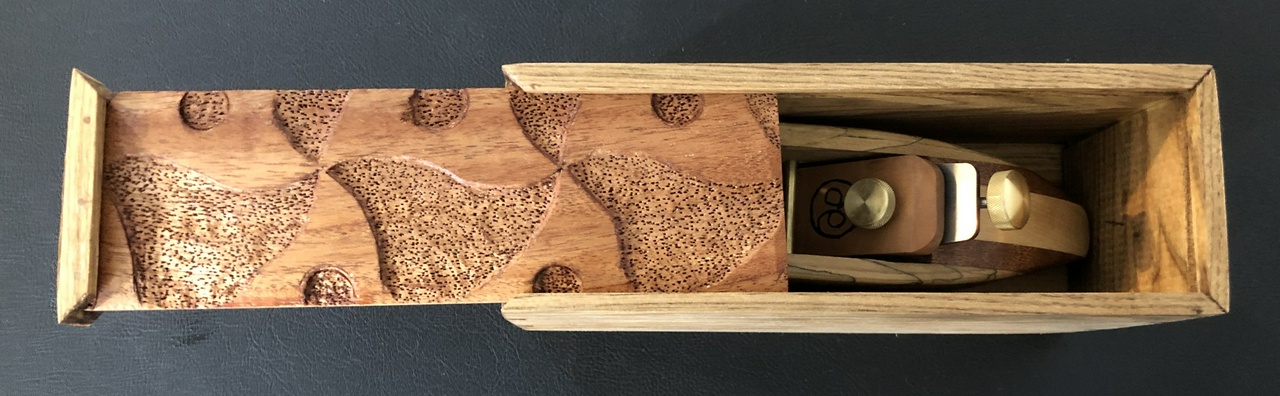
I realized after I shipped it that I don't even know the dimensions of the box. It's big enough to hold the plane, plus about 1/8 inch on the sides. The sliding lid has a 3/32 inch deep groove carved in it that makes room for the adjuster on the plane when it's as high as it can go, so the plane is very securely cradled within the box.
#woodworking #HandPlane #toolmaking #project
Discuss...
Reply to this in the fediverse: @davepolaschek@writing.exchange